Philippe Davin
Sales Manager, Bulk Solids DPT, Iteca Socadei, Aix-en-Provence, France
There are costs and there are costs …
There are different types of cost in sampling: CAPEX, OPEX, paybacks and hidden costs; the last one being more complicated to evaluate. CAPEX (capital expenditure) of a sampling station is easy to determine: the customer (end user or engineering firm) contacts us and/or our competitors to obtain a cost estimate. This should always contain more information about maintenance, and a spare part list so as to estimate OPEX (operational expenditure). Many examples have already been given to demonstrate and calculate paybacks of a bias-free sampling station in the mining industry for trade sampling. The magnitude of such paybacks are from a few hundred thousand euros to a few million euros per year depending on the commodity being produced (iron, copper, manganese, bauxite, coal etc.), plant capacity and, of course, the type of bias. Many case studies are presented in this collective Sampling Column.
All international sampling experts can confirm similar experiences as those reported below, while performing on-site measurements in order to (a) control brand new sampling solutions, (b) control existing sampling solutions to estimate inherent biases and (c) design the best sampling plan and technical approach to obtain representative samples. Because of the large numbers involved, as well as due to a high level of material heterogeneity, appropriate sampling is a well-known issue in the mining industry. Nevertheless, all the information above is necessary to convince management (technical and financial) to invest in these vital, large sampling stations.
A worst-case scenario
In a worst case, an iron ore producer ended up losing a long-term contract with his client (steel producer) because the producer was not able to guarantee the quality of the ore over several months. None of the sampling solutions installed at the producer’s port ship loading facilities complied with ISO 3082; which is the International Sampling Standard for iron ore; and neither had they been designed according to the Theory of Sampling (TOS).
But not always
Nevertheless, this is not always clear. A subcontractor was bidding for a new iron ore beneficiation plant where a sampling station compliant with ISO 3082 was required. During our technical meeting, a complete sampling station (a primary sampler and two different stages of size reduction and mass division) was presented. The project manager was looking at the drawing of the complete station and asked: “Where is the sampler?”. He did not understand that a complete station is required for the project and smiled back to us: “This is not what we need. We looked at the PID and it shows a single spoon called “Sampler”. We included €50,000 in our quote for this spoon.” He did not agree with our explanations and all our calculations and finally said: “No way”. Six months later, after all the appropriate technical aspects had been clarified between the subcontractor and the engineering firm, the project manager came back to us, requesting a quote for the complete sampling station that had been presented earlier. The final cost was more than half a million euros.
In the mineral sector
In the mineral industry, numbers and costs are at lower levels, but sampling errors and/or biases can also have important financial consequences that are equally difficult to demonstrate and evaluate at the beginning of a project: these are the hidden costs. We have listed below some examples seen in our few decades experience as a manufacturer of sampling solutions.
Case 1
A few years ago, a mineral processing plant decided to control its production along the full process of crushing raw material and screening them into specific size fractions. A few cross-belts and screw samplers were installed at various locations in order to control chemical composition. It was understood by everyone that these types of samplers do not comply with the TOS, nor any existing sampling standard and that the material collected cannot be representative. Nevertheless, analytical results were always “on target”. Was it because the chemical composition of the product was “almost homogeneous”, or because the specific size fractions collected by these non-representative samplers were the only ones of interest in the contract specifications—nobody knows!
Two years later, the plant wanted to remove manual sampling elsewhere in the plant, and management decided to install the same existing technology (screw and cross-belts), now to control product quality at their truck loading stations. The critical aspect to be controlled was the size distribution. Samples were required both for the plant’s own laboratory, as well as for their client’s.
The analytical results of these analyses were all way out-of-specs! Both laboratories went crazy. Plant management first decided to re-process some of the product already loaded in trucks (nightmare); then decided to stop the plant for few days in order to inspect all the crushers and screens to better understand the cause of this non-conformity. The plant finally had to pay penalties to its customer for non-compliance with the contractual specifications.
The explanation is easy for anyone who is familiar with the basics of the TOS: cross-belt samplers (also called hammer samplers) were not able to collect the fine material located close to the belt, and, therefore, this type of sampling technology under-represents the proportion of fines—and the screw samplers crushed down particles having a specific size fraction due to friction on particles in the gap between the rotating screw and its casing. This increased size fractions of the small particles, resulting in the reduction of the other size fractions of larger particles. This had nothing to do with the quality of material being loaded, but was due to the sampling technology that modifies the size of some particles. The client forced the plant to improve quality control in their process because they had lost confidence and the plant was finally forced to replace these non-representative samplers by appropriate representative ones. It is difficult to estimate the hidden costs of this entire issue, but the economic consequences for the plant are very clear.
Case 2
Another mineral processing plant was built at the beginning of the 2000s. There are several process stages before the furnace, which is fed by air-slide conveyors. The size distribution of the particles feeding the furnace is controlled; especially the proportion of fine particles; so as to optimise process efficiency. A “sample taker” was installed in one of the air-slide conveyors. This sampling system is composed of a single opening with a vertical pipe in the lower part of the air-slide where material is supposed to “fall” by gravity; two valves allow material to be discharged and collected.
To better comprehend the sampling issue, understanding of the working principle is necessary. An air-slide conveys material by the means of a fluidising bed. It is composed of two casings; one above each other; separated by a fluidising grid. Air is introduced in the lower part and passes through the fluidising grid so as to create the fluidising bed. The incline of the air-slide creates and guides the flow toward the discharge end of the conveyor. Due to the airflow, turbulence creates a high level of segregation, based on both density and size of particles in the product flow. The sampler in place creates an opening in the fluidising grid with a pipe going down that guide sampled material by gravity to a sample collection vessel; two gates prevent from any pressure difference in the process.
Due to this working principle, the device collects particles located close to the grid, which are always the larger and heavier ones, while the fine particles remain in the upper part of the enclosure and will consequently follow the main stream, resulting in an under-representation of these fines. Stabilising the process has always been an issue at the plant and it is understood that the existing “sampling” equipment is not able to give the process operators the necessary accurate information (content of fine particles) to optimise their process.
A decision was made to replace the existing non-representative sampler by a TOS-compliant correct sampler. Care was taken on the flow of air as well as on the limited place available to install a new sampler. This is why a new sampling solution has been especially designed to meet these special requirements. Hidden costs are also significant in this example, but complicated to estimate in details. The only solution is: representative sampling!
Case 3
Energy is critical in mineral processing plants for two main reasons: cost and CO2 emissions. In the lime industry, the process is composed of a kiln (vertical or rotary) to calcine limestone (CaCO3) in order to remove CO2 and obtain CaO (lime). Sampling at kiln discharge in order to measure the remaining CO2 content (unburnt content) gives the necessary information to optimise the kiln process in terms of product quality and to reduce energy consumption. Cross-belt solutions are popular in this industry and, as said previously in Case 2, fines are not collected (or at least most of them) which creates an important bias, because they are consequently under-represented in final sample. This results in biased measurements on the unburnt content (the smaller the particle is, the better the calcination has been).
In this plant, when a part of the production is considered as being out-of-spec, it goes to waste. This part has been evaluated and fluctuates from 5 % to 12 % of the production. In order to reduce this waste, operators increase the heating process resulting in a significant rising cost of energy. Are they going to waste because of real poor quality or only because of a poor non-representative sampler? The solution was to install a representative sampler at belt end discharge of the conveyor located directly after the kiln, in order to be as close as possible to the heating process and to reduce the lag time between sampling and analysis.
It is again difficult to estimate the hidden cost of energy when operators increase heating process, but the numbers may be significant. Nevertheless, it was easy to calculate the payback of the sampling station based on the portion of production that was wasted in this plant; payback of the TOS-compliant sampling station was within three to four months only!
Case 4
Another lime producer received claims from its customer because the remaining CO2 was out-of-spec in some specific size fractions (not all of them); and this issue was not constant over the time. A solution was found: measure the remaining CO2 at the discharge of a crusher located after the kiln, so as to control the quality of each size fraction of the lime sold to the customer. A sampling station was installed and increments screened into the different size fractions of the contractual specifications; each of these was prepared individually in order to obtain a final sample representing each of all the size fractions produced and sold.
The number of claims was reduced significantly, with an obvious commercial advantage for this plant.
Conclusions
Such hidden costs due to poor sampling are common in the entire solid bulk industry. To avoid the famous “if only I had known this before!”, knowledge of the good practices in sampling and in the TOS should be improved and increased at all different levels of management to give them all the tools to take the right technical and financial decisions. This does not necessarily mean to invest in solutions that are more expensive, but to better understand what is really necessary to meet their expectations and, thereby, stop losing money. Whatever the situation is—quality control, process control, metal accounting, trade—sampling is the first crucial step to reliable measurements and many decisions are taken based on these analytical results. It is worthwhile remembering a famous sentence of M. Pierre Gy: “On primary sampling, bias can be up to 1000 %, up to 50 % on secondary sampling, whereas it never exceeds 0.1–1 % in analysis”. Reliable (accurate and precise) analysis requires representative samples.
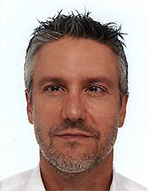
Philippe Davin
Philippe Davin has a Masters degree in Mechanical Engineering and Industrial Automation. He has worked in the mineral industry for more than 25 years with Iteca, a French manufacturer of representative sampling solutions, sample preparation, sample transport and fully automated laboratories. He is currently head of the Department for Sampling in the Mineral and Mining Industry with the responsibility of developing this market worldwide. Philippe was co-chairman of the WCSB7 (World Conference on Sampling and Blending), Bordeaux, France, in 2015.
philippe.davin@iteca.fr